Where To Find Guest Blog Writing Opportunities On Manway Gaskets.
Gasket kits come in numerous types and the kind of gasket kit you need will depend upon the sort of equipment or equipment you are working with. Whether a part of a bigger manufacturing operation, or simply involving a piece of daily equipment at your house, gasket kits are customized to fit the particular task in which you are involved.
Examples of some types of gasket kits are engine overhaul gasket kits, flange insulation gasket packages and isolating gasket kits. There are also lots of other types depending on the type of market they are required for.
Over time, gaskets will naturally start to use and break down. And this is where gasket kits play their part. These sets supply the needed replacement pieces and also consist of all the various gaskets that the corresponding piece of equipment requires. For this reason, it is also crucial to acquire a complete gasket set to ensure all of the various kinds of gaskets are offered.
THE ROLE OF GASKETS
Gaskets are a small, fitted piece which usually functions as a buffer between two larger working parts. They are made in a variety of shapes, often taking a circular or ring type, and serve as a sealant and point between two parts. Their function is to eliminate wear and friction between those corresponding parts. For this reason, gaskets appear extremely frequently in most equipment, and are http://yousher.com/kadora3211/post-of-the-punniest-32495.html utilized in whatever from cam lens protectors to different types of engines.
One function of gaskets is in their usage as sealants. As liquid seals they safeguard against leaks. Ecological seals defend against dust and other possibly dangerous particles and ecological contaminants. Anti-vibration gaskets, such as in handling sound frequencies, serve as a pad or insulant to filter those frequencies and reduce the amount of energy being wasted.
KINDS OF MATERIALS UTILIZED TO MAKE GASKETS
While gasket sets are frequently made from rubber, they are frequently made of plastic and other products as well. The materials chosen in their building are used because of their resistance to particular chemicals such as acids, or due to the fact that they can enduring severe temperatures or pressures.
Together with rubber gaskets, non-asbestos gaskets are used in several applications involving acid, steam, oil and water. Cork gaskets are used mainly in fields including oil, fuel and solvents. These gaskets are made with elastomer bindings which offer considerable versatility and compression.
Thermoplastics are thought about an upgrade from basic gasket materials considering that they tend to form a much better and tighter seal and have a longer lifespan. They also tend to be more resistant to different chemicals. While standard rubber gaskets continue to have a strong structure and function effectively in machinery, thermoplastic gaskets are worth considering for their included strength and resistance.
THE ROLE AND USAGE OF COMPRESSORS
One area in which gaskets and gasket packages are involved is within compressors. In regards to equipment, compressors are generally used to supply different types of gasses at an increased pressure. They are utilized broadly in different types of commercial fields and in numerous applications, serving in a range of various capacities and taking numerous various types.
In the refinery and gas industry, natural gas, air, refrigeration and P.E.T. compressors are an important part to those particular businesses. If the compressors and their corresponding parts are not running at appropriate effectiveness, it can permit for irregular quality, leakages and other problems which can cost these markets time and reduced revenues and can possibly affect the efficiency and efficiency requirements their clients expect from them.
REFINERY AND GAS MARKET COMPRESSOR PARTS
In relation to natural gas, air, refrigeration and P.E.T. compressors, the parts of which they are consisted of require constant attention and upkeep to make sure those systems are running at maximum effectiveness. Must any of these parts need to be replaced, it is necessary to have access to a manufacturer who focuses on and is capable of providing quality replacement parts to make sure the compressor system continues to function appropriately.
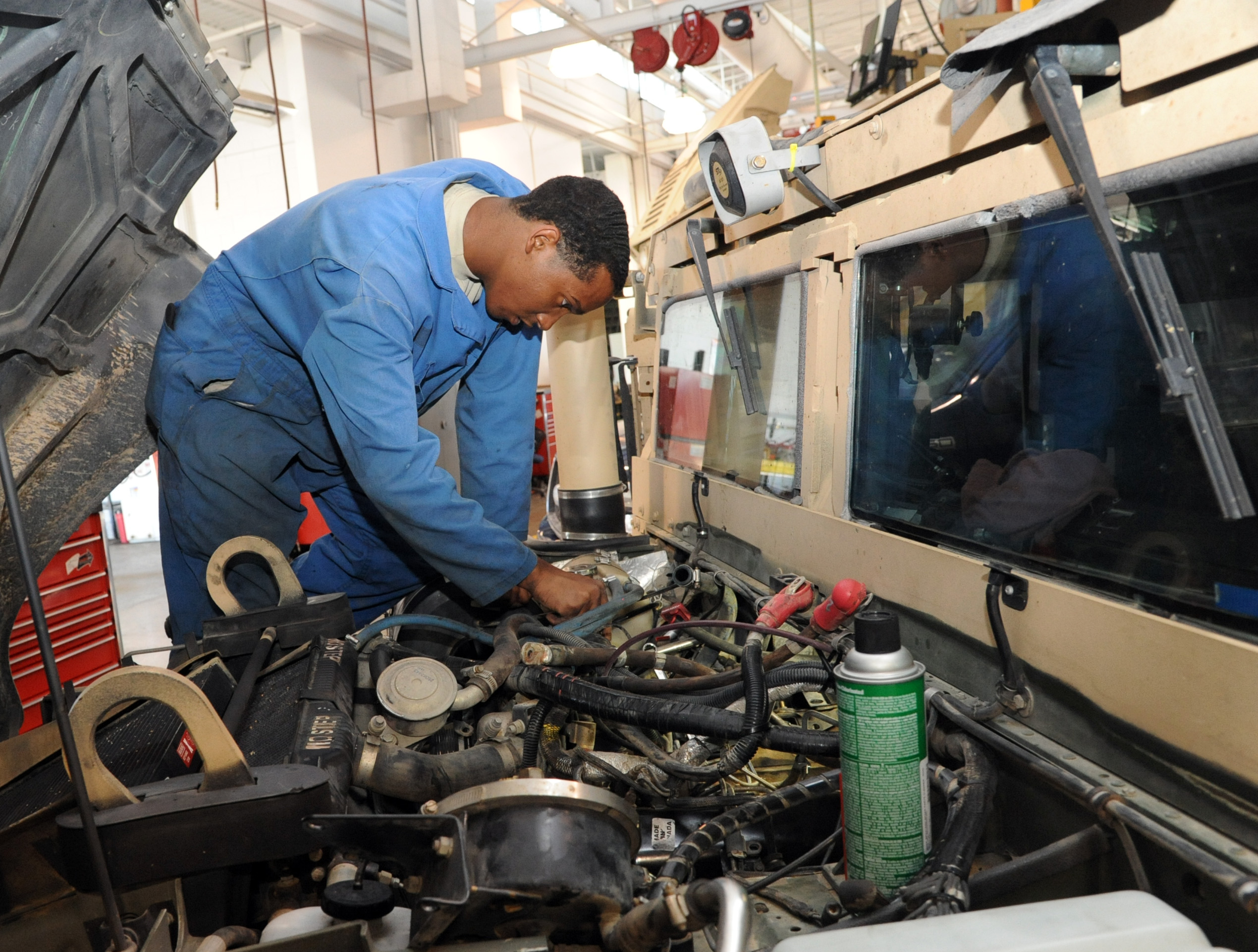
The replacement of valve parts, in particular, has specific niche positioning in this market and also requires somebody with a substantial background and matching knowledge of the role and usage of these elements. Metal plates such as wafer plates, damper plates, spring plates, valve plates and cushion plates are examples of valve parts. Along with them are High Performance Thermoplastic parts, such as plates, rings, blanks and poppets. Lantern Rings, Springs and Button/Nubs are additional examples of valve parts of which refinery and gas industry compressors are comprised.
GASKETS IN REFINERY AND GAS INDUSTRY COMPRESSORS
Gaskets are a necessary part of any compressor system. When it comes to compressors, they function as a buffer in between the parts-- such as those pointed out-- within the compressor and allow them to operate without disrupting each other and causing reverse friction and subsequent damage. Various types of gaskets are needed for various compressors. Their shapes and sizes are customized to accommodate the specific components of a compressor, depending on the kind of system and parts involved.
In the case of refinery and gas market compressors, gaskets basically play the very same function just like other sort of compressors, however their use and efficiency can be even more important given that the compressors used in these industries tend to be more complicated and likewise operate under more taxing circumstances given the environments they are put within. Chemicals, heats and other ecological elements can position extra tension on these parts as they function.
As with compressors that function in other capabilities, the truth that refinery and gas market compressors run in possibly demanding environments ties back into the importance of having a proper gasket set readily available in the event of any breakdowns. To begin with, selecting gaskets that are made of thermoplastics or other more resilient products may be a better option for these sort of compressors. It will ensure that the gaskets have a longer life-span, and in doing so that they will likewise do their part in securing the matching parts they are buffering. And, in the event of a gasket naturally using down in time, having a complete gasket set will make certain that the operator will have the correct replacement piece, therefore having the ability to make the repair quicker and efficiently and, in doing so, conserving time and expense.
Jay Turner Company
1012 N 1st St, Artesia
NM 88210, USA
575-746-1730